Fabrikken i fabrikken
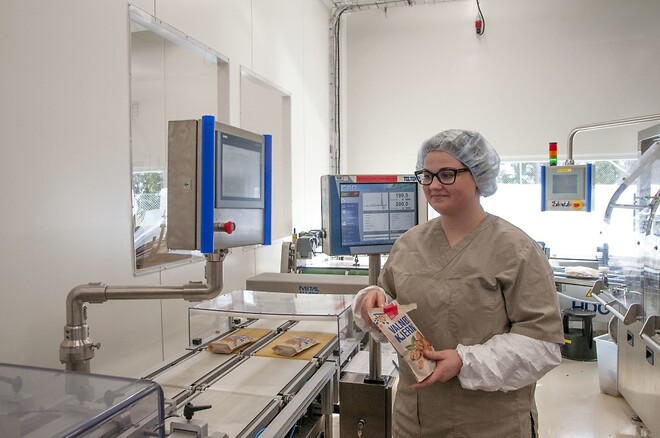
Selskapet fremstår som en fabrikk i fabrikken til kundene deres i næringsmiddelindustrien og står for blant annet resept- og emballasjeutvikling i tillegg til testing, innkjøp, blanding – og til slutt pakking.
Daglig leder Per Anders Berge formelig strutter av stolthet når han viser oss rundt i den helt nye fabrikken til Maskinpakking AS som nå er i full drift i Follestad Næringspark i Røyken. Og han har god grunn å være stolt – både av anlegget som ble designet til selskapet fra bunnen av og av selskapets kundemasse. For det er langt fra noen småselskaper som Maskinpakking betjener og som generer et årlig produksjonsvolum på rundt 4.000 tonn. Freia (Mondelēz) er den klart største, men selskapet betjener også andre store næringsmiddelprodusenter som for eksempel Fazer, Lantmännen, Unil, Idun og Axfood i Sverige.
Leverer ferdige produkter på pall
Flere vil nok undre seg over hvorfor store produksjonsbedrifter velger å outsource pakkingen.
– Mange av disse må jo ha et stort antall egne pakkemaskiner?
– Ja, det har de da også, men for enkelte av produktene deres gjør vi alt og leverer ferdige produkter på pall til dem i henhold til en 52-ukers plan, forteller Berge.
– Om ikke firmanavnet er misvisende, kan man vel i det minste fastslå at det er en kraftig underdrivelse?
– Det er riktig og vi har mange ganger diskutert om å bytte det, men folk som kjenner oss tenker ikke over det. Årsaken til navnevalget var forøvrig at håndpakking var det vanligste da selskapet ble etablert på Kampen i Oslo i 1953 og tok i bruk maskiner til pakking.
Per Anders Berge har lang bransjeerfaring og hadde blant annet vært daglig leder for Nor-Reg i åtte år da han ble ansatt som daglig leder i Maskinpakking i 2002. Da kjøpte han samtidig 49 prosent av aksjeposten i selskapet. De resterende aksjene var eid av grunnleggerens sønn, Jan Tomas Kjendlie, men etter at han senere solgte seg ut er selskapet nå eid av Berge med 75 prosent og av markedssjef Ketil Snarset med 25 prosent.
Konsentrerer seg om næringsmiddel
Maskinpakking har rundt 40 ansatte og produksjonen foregår over to skift i tillegg til en del nattskift. Tidligere hadde selskapet kunder i flere bransjer, men i 2010 valgte de å legge ned non-food-virksomheten. Fem år senere kuttet de også ut legemidler, dels fordi Nycomed valgte å flagge ut mye av sin virksomhet. I forbindelse med flyttingen la Maskinpakking også ned farmabiten slik at virksomheten nå i all hovedsak er konsentrert om næringsmiddel.
Berge forklarer at dette ble gjort for å gjøre selskapet best mulig konkurransedyktig.
– Så lenge kundene forventer at vi leverer et ferdig produkt, betyr det at vi også må stå for innkjøp av råvarer – og for enkelte av dem også utvikle resepter. Dette krever så mye ekspertise at det ikke lenger var mulig for oss å gjøre dette på en god måte hvis vi hadde operert i flere kategorier, sier Berge, som viser til at innkjøp ofte står for 60 prosent av salgsprisen.
Men også reseptene utvikles ut fra et økonomisk fokus. Foruten å komme frem til en best mulig smak på selskapets laboratorium og prøvekjøkken, forteller Berge at de samtidig er veldig fokusert på hva ingrediensene koster. Under utviklingen av nye resepter gjennomføres alltid blindtester, hvor det for eksempel kan komme frem at ingen merker forskjell på om det er 12 eller 14 prosent innblanding av en råvare.
Eksperter på emballasje
– Emballasje er det vi kan ekstra godt, fastslår Berge, og legger til at selskapet alltid gir kundene råd om kvalitet, barriere, design, fyllingsgrad, hylle- og palleoptimalisering, pris etc. Flere av selskapets emballasjeløsninger har vunnet bransjepriser, både den skandinaviske ScanStar- og den verdensomspennende WorldStar Packaging Award.
Berge forteller at selskapet har en tung teknisk avdeling som optimaliserer, tilpasser og kobler sammen opptil fire til seks ulike maskiner til en komplett pakkelinje. For én av kundene pakkes det kakao i sjaktler til hele Norden. Da denne ønsket å gå over til en flip top, som kunne åpnes som en sigarettpakke, bygget de maskinen selv.
– Får produsentene av pakkemaskinene utnyttet kompetansen dere har på dette området?
– Ja, det gjør de. Vi har for eksempel lenge hatt et nært samarbeid med vår leverandør av hovedmaskiner, tyske HDG som er størst i Europa på sitt område. De produserer maskiner som skal fylle poser raskest mulig, men tenker ikke alltid på utfordringene brukeren har i hverdagen. Det er for eksempel helt sentralt for oss å redusere nedetidene til et minimum når maskinene må vaskes helt ned i forbindelse med bytte fra ett allergen til et annet, og resultatet ble vesentlige forskjeller på den vi fikk være med å utvikle og den eldre versjonen vi har av samme maskin.
Mange pakketeknikker
Til tross for alt dette er fortsatt pakking hovedvirksomheten. Etter å ha faset ut mange av maskinene som ble brukt på virksomhetsområdene som nå er kuttet ut, har selskapet syv pakkelinjer i tillegg til at det er planlagt og satt av plass til ytterligere to.
Berge forteller at de fyller og pakker rundt 200 ulike produkter. 90 prosent av disse er forbrukerløsninger, resten er til storhusholdning.
– Vi tilbyr de fleste pakketeknikker, men hovedsatsingen er mot ståposer som ofte har rivehakk en zip-lukkemekanisme, flatposer, sjaktler uten innerpose og poser i sjaktel (multipack). Ikke minst har vi mye fylling direkte i en primærsjaktel som er kledd innvendig med PE og med membran i bunn og på topp. En slik løsning er det ikke mange som driver med, men etter min mening er det en optimal løsning med en firkantet boks som gir god barriere i tillegg til at den er rimelig siden den ikke trenger en innerpose. Fyllingsgraden bedres når man unngår innerposen og dobbel emballasje medfører jo både dårlig økonomi og logistikk, sier Berge, som også viser oss eksempler på smarte D-pakløsninger de har utviklet og som i vesentlig grad forenkler arbeidet til de ansatte i butikkene.
– Når man utvikler et nytt produkt er det vanskelig å vite hvor lang holdbarhet man skal sette på det. Vi gjennomfører derfor også omfattende akselererte Shelf life-tester av disse i emballasjen og som i løpet av bare en åttendedel av den reelle tiden fastslår produktets holdbarhet.
Fra Slemmestad til Røyken
Maskinpakking holdt tidligere til på Slemmestad. Lokalene der var langt fra ideelle, med blant annet svært lange kjøreveier. For å oppnå bedre lønnsomhet og økt fleksibilitet i produksjonen ønsket Berge lenge å flytte, men ble holdt igjen av den tidligere eieren og styreformannen som også eide bygget de holdt til i. Da han til slutt trakk seg ut i 2016 inngikk Maskinpakking raskt en opsjonsavtale med det kommunale selskapet Røyken Eiendom om en tomt i Follestad Næringspark, ca. 15 kilometer sørover på Hurumlandet og med en svært gunstig plassering tett inntil riksvei 23 med Oslofjordtunnelen et steinkast unna.
Berge forteller at de prioriterte å investere i drift og maskiner fremfor i eiendom, og etter at de hadde fått byggetillatelse inngikk Maskinpakking en avtale med Ticon Eiendom som skulle sette opp bygget samtidig som det ble inngått en langsiktig leieavtale på ti år med opsjon på ytterligere fem pluss fem.
Samtidig fikk Maskinpakking en 5-årsavtale med Freia som dermed ville sikre en jevnt høy aktivitet også de to første årene i det nye bygget, som for øvrig stod klart i oktober i fjor.
– Freia er kjent for å være en av de mest krevende kundene som finnes. Gjennom 40 år har deres strenge krav vært med på å løfte oss slik at også vi har blitt bedre, sier Berge, som uttrykker takknemlighet for at de fikk en lengre avtale enn de tre årene som ellers er vanlig.
Bortsett å fra å leie inn et par ekstra teknikere stod Maskinpakking selv for den omfattende flytteoperasjonen.
– I forkant hadde vi produsert opp ekstra til kundenes egne ferdigvarelagre og deretter flyttet vi en og en linje mens vi hadde full produksjon og logistikk på to steder. På det mest intense kjørte vi tre skift på Slemmestad og to her på den nye fabrikken. På den måten reduserte vi produksjonsavbruddet til et minimum, forteller Berge.
I slutten av januar flyttet de for godt ut av de gamle lokalene i Slemmestad og noen uker senere var alle de syv pakkelinjene i den nye fabrikken operative.
Utnytter tyngdekraften
Det nye bygget ble designet og skreddersydd for selskapet helt fra starten av og Berge forteller at de tenkte logistikk hele veien. Bygget er på 4.200 kvm, men tomten er stor nok til at det kan utvides med mer enn 1.000 kvm samtidig med at det fortsatt vil være gode utearealer til å ta imot store lastebiler.
Fra varemottaket fraktes råvarene rett opp i annen etasje. De kommer som regel i 1.000 kilos storsekker som dels lagres i reoler eller rett på gulvet som er dimensjonert for å tåle en belastning på hele 2.5 tonn per kvadratmeter.
Her finnes det også et svaltlager til råvarer som må lagres kjølig og fyllerom til hver pakkelinje i etasjen under. I fyllerommene henges storsekkene opp i et stativ før tyngdekraften overtar. Råvarer som skal blandes løftes med truck ytterligere noen meter opp på et galleri hvor det er et blanderom. Etter å ha gått gjennom blanderen overtar de samme naturkreftene med å få den ferdige blandingen ned.
– I første etasje har vi elleve produksjonsrom som alle separert med kun ren luft og regulering av temperatur og fuktighet. Pakkingen i ytteremballasje skjer enten inne i de samme rommene eller ute i fellesarealet, forteller Berge, som opplyser at denne etasjen også blant annet har et eget rom for allergenvask av demontert utstyr og et lager for maskindeler.
Når pakkingen er ferdig blir de palletert på stedet og transportert den svært korte veien over til ferdigvarelager av operatøren som betjener linjen. Berge opplyser at de vurderer automatisk pallettering og eventuelt ha én operatører på to linjer, men at det ligger et stykke frem.
Kompakt og effektiv logistikk
I planleggingsfasen av den nye fabrikken var Maskinpakking i kontakt med flere leverandører av lagringsløsninger, men Berge forteller at de valgte å gå videre med Jungheinrich – hovedsakelig basert på de at tilbød en god løsning, men også at de hadde god erfaring med denne leverandøren fra før. For noen år siden ba Maskinpakking om hjelp av dem til å finne frem til en løsning for å ta storsekker inn i de lave fyllerommene i den gamle fabrikken. Den utfordringen ble løst enkelt ved bare å snu gaflene på en EJD ledestabler.
Ragnar Pettersen, salgssjef Logistic Systems, og salgskonsulent Espen Fristad i Jungheinrich Norge uttrykker naturligvis glede for at selskapet ble engasjert i også å finne en løsning for lagring av hovedsakelig ferdigvarer og emballasje i første etasje, og Pettersen satte stor pris på å komme inn på et så tidlig stadium i prosessen at det nesten ikke fantes tegninger.
Han forteller om en tett og god dialog med både bruker og arkitekt, hvor de gjennomdiskuterte flere løsninger før de til slutt endte med en kombinasjon av kompaktlagring for nær 490 paller med ferdigvarer og 950 paller til emballasje og annet i konvensjonelle reoler. Det er en økning på 50 prosent sammenlignet med hva selskapet hadde på Slemmestad.
Berge legger ikke skjul på at han i begynnelsen var noe skeptisk til kompaktlagring, men etter blant annet et referansebesøk hos Kransekakebakeren ble han overbevist. Så langt er han meget godt fornøyd med denne løsningen som gir plass til nesten dobbelt så mange paller på samme areal som med konvensjonelle reoler. Anlegget har to shuttler, men den ene benyttes kun ved topper og er ellers i reserve.
Øverste pallenivå i begge reolanleggene ligger på 10,25 meter og blir betjent av en nyanskaffet skyvemasttruck av typen Jungheinrich ETV 214. På grunn av den store løftehøyden er den utstyrt med tilleggspakken liftPLUS, i tillegg til både å ha gaffelkamera og forhåndsprogrammerte løftehøyder. I forbindelse med flyttingen gikk Maskinpakking også til anskaffelse av en brukt, men nullstilt ledetruck av typen Jungheinrich EJE, men utover det er den relativt beskjedne truckparken av eldre dato, inkludert en skyvemasttruck nede. Den har en løftehøyde på bare fem meter og har dermed et begrenset bruksområde.
Råvarelageret i andre etasje er inntil videre innredet med de konvensjonelle reolene som Maskinpakking tok med seg fra Slemmestad. Det betjenes av en eldre motvektstruck som krever stor gangbredde og i tillegg utnyttes på langt nær hele takhøyden. Likevel er lagringskapasiteten også av råvarer blitt økt med 50 prosent. Det betyr at selskapet nå har anledning til å kjøpe inn større mengder enn tidligere, men planene om en mer effektiv reolløsning også i denne etasjen er såpass konkrete at Maskinpakking har tegnet opsjon på ytterligere en skyvemasttruck.
Berge er svært tilfreds med at kjørelengdene i den nye fabrikken – både fra råvarelager til produksjon, derfra til ferdigvarelager og videre de få meterne ut til rampe – er blitt redusert med nærmere 60 prosent sammenlignet med hva de slet med tidligere.
Ny it-løsning til neste år
På hjemmesidene sine mener Maskinpakking at de har bygget «Nordens mest avanserte produksjonsfabrikk», men likevel er det en vesentlig og viktig oppgradering som gjenstår: Axapta. Bare navnet indikerer at forretningssystemet er av eldre dato, men Berge bedyrer da også at de til neste år skal starte prosessen med å innføre et nytt. Da vil det også bli innført terminaler på alle linjene som skal erstatte dagens papirbaserte rutiner. Selskapet vil da høyst sannsynlig også oppgradere seg til sD2-logistics fra APX Systems – arvtakeren til superDAGFINN som selskapet tok i bruk for ti år siden til styring av merkemaskiner og utekspedering med avansert pakkseddel.
Stor eksportandel
Det er ikke mange årene siden Maskin-pakking hadde 80 ansatte, men stadig høyere automatiseringsgrad har medført en tilnærmet halvering samtidig med at omsetningen er beholdt. Berge opplyser at den i år vil ligge på rundt 130 millioner kroner, hvorav eksport står for om lag 40 prosent. Det i seg selv er et godt bevis på hvor konkurransedyktig virksomheten er. Maskinpakking har for øvrig et datterselskap i Sverige, riktignok uten ansatte.
– Hvis vi skal kunne konkurrere utenfor landets grenser kan vi dessverre ikke benytte norske avgiftsbelagte varer. Eksempelvis er eggepulver dobbelt så dyrt i Norge som det er i Sverige.
Derfor tar vi inn en del råvarer derfra for midlertidig bearbeiding og som deretter eksporteres. Men kakaoen som vi pakker for alle de nordiske landene kan vi kjøpe inn direkte fordi det ikke er i konkurranse med norske bønder, avslutter Per Anders Berge med et smil.
Foreløpig i hvert fall, legger vi til. Med den varslede globale oppvarmingen skal man aldri si aldri.
Maskinpakking ASMaskinpakking AS ble etablert på Kampen i Oslo i 1953 av Jan Kjendlie og er landets ledende aktør innen kontraktproduksjon og pakking. Selskapet hadde tidligere kunder innenfor både næringsmidler, non-food og farma/legemidler, men konsentrerer seg nå kun om produksjon av næringsmidler som leveres ferdig palletert. Virksomheten omfatter reseptutvikling, innkjøp, emballasjeutvikling, blanding, pakking og akselerert Shelf Life testing. Maskinpakking fyller og pakker rundt 200 ulike produkter og årsproduksjonen er på rundt 4.000 tonn. Selskapet har ca. 40 ansatte, omsetter for om lag 130 millioner kroner og har nylig tatt i bruk en helt ny fabrikk i Røyken på Hurumlandet. |