Motor Part: Økt produktivitet på halvert lagerareal
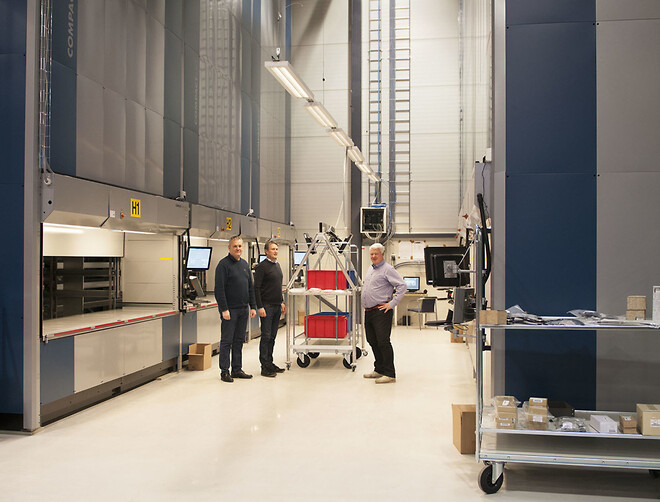
Det norske personbilsalget i fjor ble det høyeste på 30 år. Sammenlignet med 2014 økte antall førstegangstregisterte biler i 2015 med 4,5 prosent. Motor Gruppen AS kunne glede seg over at salget av Mitsubishi økte med over 10 prosent og ikke minst at Renault virkelig skjøt i været med en vekst på hele 64 prosent sammenlignet med 2014.
Gruppens logistikkselskap, Motor Part AS, importerer, markedsfører og distribuerer reservedeler, utstyr og rekvisita til i alt 90 forhandlere og servicepunkter. Selskapet ble etablert i 1982, syv år etter at de første Mitsubishibilene ble solgt i Norge, og har siden 1985 holdt til i Hokksund. Det var for øvrig midt i Mitsubishis desiderte glansperiode her i landet, der spesielt Pajero og Galant bidro til at merket lå svært høyt oppe på registeringsstatistikkene. Det bidro til at lageret i Hokksund ganske raskt ble doblet til 7.500 kvm, inkludert kontorer til både dem selv og søsterselskapet Motor Data.
– Vi hadde likevel veldig god plass i Hokksund, fastslår Jan-Erik Moe. Han har fulgt selskapet siden starten av og er i dag distribusjons- og lagersjef. – Men så var også logistikken helt annerledes den gang med blant annet lange ledetider fra Japan der vi fikk alle delene fra, legger han til.
I 1994 etablerte Motor Part det første tollfrie lageret her i landet. Bakgrunnen var at de den gang også betjente alle de danske Mitsubishiforhandlerne. Driften var så veltrimmet at Mitsubishi i Japan to år senere utnevnte Motor Part som verdens beste ettermarkedsselskap. Avtalen med Danmark ble avsluttet i 1998 i forbindelse med etableringen av et europeisk sentrallager i tilknytning til Mitsubishis bilfabrikk i Born i Nederland.
Motor Part har opp gjennom årene håndtert deler til flere forskjellige bilmerker. Foruten Mitsubishi er selskapet i dag ansvarlig også for Renault som Motor Gruppen overtok importen av i 2010 og Dacia som kom inn i 2013.
Ville finne mer egnede lokaler
I tillegg til den store lagerflaten som medførte lange kjøreveier, ble alt plukket i Hokksund foretatt manuelt. De mange småvarene var plassert i et smalgangslager, bestående av fire reolganger i 50 meters lengde og åtte meters høyde.
Nordverk Norge er en av landets ledende leverandører av lagerautomater og selskapets salgssjef Nils Brekka banket på døren til Motor Part allerede i 2011 og argumenterte for automatenes fordeler når det gjelder plukkeffektivitet av småvarer. Det andre hovedargumentet om plassbesparelse var ikke verd å nevne der oppe, men selv etter et omfattende analysearbeid takket Motor Part nei.
Selskapet ble imidlertid mer og mer klar over gevinstene ved å komprimere lageret og i fjor ble det besluttet å ikke fornye leieavtalen.
– Bakgrunnen for å flytte Motor Part fra Hokksund var et ønske om å få mer rasjonelle og effektive lokaler. Dette er viktig, ikke minst med tanke på å bevare hovedlager for deler og utstyr til bilmerkene vi importerer i Norge. I konkurranse med andre løsninger for distribusjon av deler og utstyr til forhandlerne våre må vi alltid arbeide for å sikre mest mulig kostnadseffektiv drift, forteller daglig leder Glenn Løvlie.
Motor Part tok en beslutning om å flytte ut i desember samme år, men visste på daværende tidspunkt hverken hvor eller hvordan det nye lageret skulle se ut.
Uten heller å ha bestemt seg for om de skulle satse på automater eller ei, ble Nordverk Norge leid inn for å analysere hvor mye plass Motor Part trengte. Siden sist Nils Brekka hadde vært i kontakt med Motor Part hadde de bygget ned lageret fra rundt 35.000 artikler til 21.000, hvorav 13.000 var småvarer.
– I tillegg fikk vi vite hva som ytterligere skulle bygges ned, men vi hadde jo ikke peiling på hvor mye nytt som eventuelt ville komme. Det ble derfor mye gjetting på tall, forteller Brekka.
Underveis ble det kjent av det gamle lagerbygget til Kid Interiør på Gulskogen i Drammen ble ledig. Det er betydelig større enn de ca. 3.500 kvadratmeterne Brekka hadde kommet frem til ville være passende til lager, men Motor Part og moderselskapet kom i fellesskap raskt frem til en plan om å flytte deler av virksomheten fra hovedkontoret i Oslo til Gulskogen.
I mai, altså bare syv måneder før Motor Part måtte ut fra Hokksund, besluttet selskapet å gå for Kid-bygget og tegnet en avtale med Nordverk Norge som totalleverandør av lagerinnredningen.
Dårlig gulv skapte tidsnød
For å ha færrest mulig prosesser på lageret var layouten til Nordverk Norge basert på to hovedløp etter varemottaket: Samtlige 13.000 artikler med småvarer skulle plasseres i seks Compact lagerautomater, mens majoriteten av de øvrige skulle legges inn i et svært kompakt smalgangslager med plukk fra utskyvbare trekasser. I tillegg ville en del karosserideler og andre større komponenter bli lagret på pall i konvensjonelle reoler. Ordrene skulle til slutt pakkes og sammenstilles på et avsatt terminalområde.
Tiden frem til sommeren ble brukt til videre analysearbeid og ikke minst utarbeidelse av en fremdriftsplan. Den var i utgangspunktet stram for Nordverk som fikk en kjempeutfordring dra de skulle starte å montere.
– Da viste det seg at den delen av bygget stod på søyler og at betonggulvet ikke holdt mål. Dette var ukjent for utleieren Brække Eiendom som nylig hadde kjøpt bygget av Kid, og flere måtte kaste seg rundt, forteller Nils Brekka mens Jan-Erik Moe nikker sympatiserende med hodet. – Dermed måtte vi forandre layouten og tilpasse plasseringen av både reoler og automater til der søylene stod, i tillegg til at det måtte legges store stålplater under automatene som kunne fordele vekten over en større flate. Dette ødela nattesøvnen for noen av oss, men takket være kreativ og løsningsorientert innsats fra mange kompetente fagpersoner ble det likevel bra, legger Brekka til.
Flying start
Motor Part la ned driften i Hokksund den 18. desember. Forhandlerne hadde da naturligvis i god tid på forhånd blitt informert slik at de kunne bygge opp sine egne lagre. Mandag 4. januar braket det løs på Gulskogen og selskapet fikk virkelig en flying start.
– Den første dagen lagerautomatene ble tatt i bruk plukket en av medarbeiderne 250 artikler på en time mot mellom 50 og 60 på Hokksund. Overfor Motor Part hadde vi skissert rundt 200 i timen når de var blitt innkjørt, så vi ble veldig positivt overrasket, sier Nils Brekka, og Jan-Erik Moe er så enig så enig.
– Jeg hadde forberedt medarbeiderne på at de måtte innstille seg på en ny hverdag med nye rutiner, men da vi registrerte den oppstarten så var det nærmest et rungende halleluja her.
Foruten gevinsten gjennom et langt mer effektivt plukk av småartikler har Motor Part også kunnet halvere antallet kostbare ordreplukktrucker. Det i seg selv er et viktig element i paybacken.
– I Hokksund hadde vi åtte smalgangs plukktrucker som ble brukt på hele lageret og med til dels lange kjøreavstander. I tillegg hadde vi to i reserve som ble tatt i bruk ved topper. Nå har vi gått til anskaffelse av én ny skyvemasttruck til pallhåndtering og fire nye plukktrucker av samme type som vi hadde. De benyttes bare i smalgangslageret og siden de er slingestyrt har vi kunnet gå betydelig ned i bredden på reolgangene og gjort det svært kompakt, forteller Moe.
Den nye driftsformen har også medført at bemanningen på lageret er redusert fra 17 til 11, men ingen er blitt sagt opp. Moe opplyser at lageret driftes fra kl. 8 til 17 og at de i mange år har praktisert jobbrotasjon slik at flest mulige kan kunne gjøre mest mulig.
– Det er en stor fordel ved både ferieavvikling og sykdom, men er også motiverende for medarbeiderne å ha variasjon i arbeidet. Alle skal derfor kunne betjene lagerautomatene, sier Moe.
Effektivt batchplukk med nyutviklet portal
De seks lagerautomatene er ca. 10 meter høye og, 3,6 meter lange og 3 meter dype. Det betyr at det samlede gulvarealet de opptar er på snaue 65 kvadratmeter. Til sammenligning var smalgangslageret i Hokksund der de samme artiklene ble lagret på rundt 400 kvadratmeter.
Som vanlig er hos brukere med flere automater, er de også hos Motor Part plassert i to rader med alle plukkåpningene ut mot et område på midten.
– I forkant hadde vi work shops med brukerne hvor vi diskuterte rutiner og hva de så for seg som de mest optimale. Vi ble raskt enige om at man ville oppnå høyest effektivitet med batchplukk og til langt flere om gangen enn til bare to kunder som ble foretatt i Hokksund, forteller Brekka.
Enda mer effektivt har de kommet frem til at det blir dersom begge plukkerne, som hver seg betjener tre automater, går sammen om opptil åtte kunder ad gangen.
– Derfor har vi laget en portal med touchskjerm på hver side og som settes over plukktrallen med kasser. Skjermen på automaten kan eksempelvis gi beskjed om at det skal plukkes ti artikler ut av heisen. Deretter snur de seg mot portalen og på den skjermen får de vite hvordan de skal fordeles på de åtte batchene. Bakgrunnen for dette er at mange av forhandlerne skal ha den samme artikkelen og ved hente ut alle av automaten på en gang sparer man mye tid, forklarer Nils Brekka.
Langvarig samarbeid med IT-leverandøren
Motor Part har i snart 25 år hatt et svært nært samarbeid med Microsoftpartneren Peritus. Så tett at selskapets daglige deler, Leo Rosbach, i en årrekke har tilbragt to til tre dager fast i uken hos dem.
I 2001 tok Motor Part i bruk forretningssystemet Axapta fra danske Damgaard – forløperen til Microsoft Dynamics AX som de i dag benytter. I 2009 utviklet Peritus en håndterminalløsning til Motor Part som i stor grad rasjonaliserte varemottak og plukk. Warehouse Streamliner gir full kontroll over lageret i sanntid, og er senere også blitt tatt i bruk av andre kunder til Peritus.
– Logistikkfunksjonen i Dynamics AX er som å balansere på en knivegg. Den ene er kapitalsiden som skal være så minimal som mulig, men det skal ikke gå ut over leveringsgraden. Bare man spiller Dynamics AX riktig, har man et optimalt balansepunkt, sier Jan Willumsen, salgs- og markedsdirektør i Peritus.
– Mange hevder at forretningssystemer generelt er svake på logistikk og at mange brukere derfor er avhengig av et eksternt WMS. Men du mener altså at det ikke er tilfelle med Dynamics AX?
– Ja, jeg vil hevde at man ikke trenger det, sier Willumsen.
– Systemet har i hvert fall bidratt til å gi oss full kontroll på alt, sier Moe. –Resultatet er blant annet en betydelig nedgang i feilsendinger og feilplukk som siste to årene ligget på mellom 0,03 og 0,04 prosent.
– Lagerautomatene vil kanskje bidra til en ytterligere reduksjon?
– Det er jo ikke mye å forbedre, men vi er likevel sikre på at det skje, sier Brekka. – Etter vår oppfatning er imidlertid ingen forretningssystemer gode nok til å kunne styre lagerautomatene våre. Derfor har vi også hos denne brukeren installert Logia WMS fra danske Logimatic som vi har benyttet i en årrekke.
Selv om Nordverk Norge har en rekke andre brukere som benytter Dynamics AX, er Motor Part den første kunden de har sammen med Peritus. Både Brekka og Rosbach fremhever det gode samarbeidet de har hatt, inkludert kontakten med Logimatic.
– Det er alltid noen tekniske utfordringer når man skal få to forskjellige systemer å snakke sammen, men det har vi fått til, sier Rosbach.
– Har dere opplevd andre større utfordringer i forbindelse med flyttingen rent bortsett fra integreringen mot lagerautomatene?
– Det har vært en veldig stor prosess. Helt siden etableringen har Motor Part operert med én lokasjon per vare. Det har derfor vært en voldsom operasjon å få alle varene lagt inn i det nye lageret. Det er fortsatt noen utfordringer, men nå begynner det å se veldig bra ut, legger han til.
Velorganisert flytteprosess
Det gode salget av både Mitsubishi og Renault det siste året medførte at Motor Part lå inne med et makslager da de skulle flytte. Stikk motsatt av hva de hadde forventet.
– Vi trodde vi skulle flytte i en god periode, men salget av både Mitsubishi og Renault medførte at vi oppnådde den nest beste omsetning i desember, forteller Glenn Løvlie. Han overtok som daglig leder av Motor Part ved nyttår, men hadde likevel tatt aktivt del i flyttingen og fullroser alle ansatte for en formidabel innsats.
– De fleste jobbet fire helger på rad i desember, i tillegg til tredje juledag. Da vi besøkte det nye lageret et par dager etter åpningen var de ennå ikke kommet helt i mål. Varemottaket var helt sprengt i påvente at alle deler skulle komme på lokasjon og de ansatte måtte innstille seg på nok en jobbehelg.
En innleid semitrailer kjørte over 50 turer mellom Hokksund og Gulskogen i desember.
– Samtlige 30 ansatte jobbet skulder ved skulder med et felles ønske om å få gjort jobben på best mulig måte. Noe av hemmeligheten med en slik flytting er at ikke nytter å banke ut mest på den ene siden for da får man raskt stopp på mottakerstedet. Ved bare å bruke en bil fikk vi god tid til å håndtere varene på Gulskogen før et nytt lass ankom, forteller Løvlie.
Her var det også til svært stor hjelp at alle varene som hadde ligget på hyller i Hokksund ble transportert i lokasjonskasser.
Foruten å rette en stor takk til sin kollega Jan-Erik Moe for god planlegging, mener Løvlie det var av stor betydning å spille på lag med Nordverk Norge som har vært med på mange tilsvarende flyttinger av andre kunder og satt på verdifull erfaring.
– Likeledes er det svært viktig å være forut på IT-siden. For oss var det av stor betydning at både Peritus og Logimatic var tidlig inne. Dette ble veldig mange pene ord, men det er på sin plass. Uten den store innsatsen fra både våre medarbeidere og leverandører hadde vi ikke klart å sende ut varer første virkedag i januar, fastslår Løvlie.
Mange funksjoner flyttes til Gulskogen
Foruten å rasjonalisere driften i Motor Part, forteller Løvlie at det også var et ønske å koble denne virksomheten bedre sammen med importanlegget på Risløkka i Oslo som konkurrerer om kapasiteten på anlegget med bilforhandleren Motor Forum Oslo.
– Spesielt ønsket vi å sikre god nok kapasitet til å gjennomføre all kursaktivitet som vi både er pålagt av fabrikkene og selv ønsker å gjennomføre. Vi arbeider stadig med å oppskalere treningsaktivitetene, ikke bare innenfor det tekniske området, men også andre typer trening og utviklingsaktiviteter innenfor salg, administrative funksjoner og ledelse, sier Løvlie og tar oss med på en rundtur i de andre delene av bygget hvor det blant annet er blitt innredet ca. 1.500 kvm kurs- og treningsfasiliteter. Av disse vil teknisk avdeling for Mitsubishi og Renault disponere rundt 900 kvm verksteder, skolerom, møterom og kontorer. De resterende vil bli tilpasset annen skole og kursvirksomhet.
– Etter å ha sett hva som brukes av ressurser på å tilrettelegge og gjennomføre større konferanser, som for eksempel forhandlermøter, mente vi også at det kunne være hensiktsmessig å legge flere av denne type arrangementer til «eget hus». På Gulskogen etablerer vi derfor også et topp moderne auditorium med plass til ca. 100 personer i tilknytning til et «show rom» for begge merker inklusive et eget «Motor Gruppen museum», forteller Løvlie, som mener dette vil gi dem anledning til å ha mer permanente utstillinger som viser den slik de ønsker det skal se ut hos forhandlerne sine.
– Alt du har sett nå, sier Løvlie på tampen av rundturen, – inklusive lageret, er på drøye 6.200 kvadratmeter. I Hokksund hadde vi 7.500, så dette er særdeles kostnadseffektivt, avslutter han.
Motor PartMotor Part AS importerer, markedsfører og distribuerer reservedeler, utstyr og rekvisita for bilmerkene Mitsubishi, Renault og Dacia på det norske markedet. Selskapet omsetter for ca. 300 millioner kroner og har 30 ansatte. Motor Part er en del av Motor Gruppen AS som også består av importselskaper for de tre bilmerkene. I tillegg driver konsernet de to bilforhandlerkjedene Motor Forum og Thrane Steen. Motor Gruppen har ca. 500 ansatte, en omsetning på ca. tre milliarder kroner og er eid av familien Thrane-Steen. |