TUNG LAGERSUKSESS: I disse strøm og miljøtider lukter det suksess av slikt - lavere kostnader og bedre miljøregnskap.
Automatisering av lageret har vist seg å være mer energieffektivt av flere grunner:
Effektiv vareflyt: Reduserer behovet for interntransport.Regenerering av energi: Automasjonsløsninger regenererer energien.Optimalisert lager...
OPPDATERT om Bohus på Heia: Norges kuleste møbellager har spart store mengder energi
Fra juni 2021 til juni 2023 har Bohus-lageret gått fra 100 prosent manuell drift til et helautomatisert kranlager. Energibesparelsen har vært 190.000 kWt, eller 17 prosent nedgang uten endringer i totalvolumet av varer.
17
Bilder
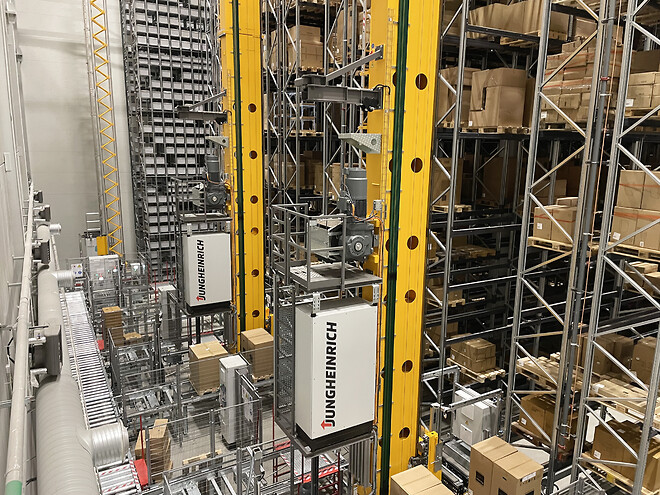
Nå viser det seg store energibesparelser med automatisering: Krananleggene til Bohus var de første som Jungheinrich leverte i Norden. Nærmest ser vi to av de tre kranene som håndterer helpall og lengst bort skimtes miniloadkranen. Foto: Henning Ivarson
Vil du ha tilgang til alt?
Kjøp et abonnement
Utforsk abonnementsløsningene våre og velg den som passer dine behov.
Velg ditt abonnement